直流电机换向故障的全面处理讲解
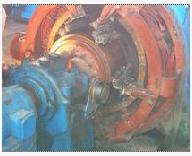
一、火花产生原因和等级
(一)换向火花划分原则
保持电刷与换向器良好的工作状态,保持优良的换向性能是保证直流电机安全的重要条件。通常情况下,电机无火花运行(或微弱的无害火花下运行),换向器表面氧化膜均匀而有光泽,电刷与换向器磨损轻微等均可认为是良好的换向性能的表征。相反,强烈的换向火花,换向器表面氧化膜破坏或异常,电刷与换向器之间滑动接触不稳定,电刷与换向器的异常磨损等都是换向不良的症状,将直接威胁电机运行。
火花是电刷与换向器之间的电弧放电现象,是直流电机换向不良的最明显标志。由于轻微的电刷火花释放能量微弱,不会构成对电机运行的危害,故称无害火花。较强的电刷火花其能量将会破坏电刷与换向器之间的滑动接触,灼伤电刷镜面和换向器表面氧化膜,使两者磨损增加,并造成恶性循环,这种火花属有害火花。更有甚者,由于强烈的电刷火花使电刷磨道上空气游离,因电弧飞越而导致环火事故对电机造成巨大的损坏,构成对直流电机运行的威胁。
不同的换向火花对直流电机运行的影响和危害不同,为了确定换向火花对直流电机运行的影响和危害,必须要划分火花等级。
换向火花是电刷和换向片脱离接触时换向元件中释放电磁磁量,以电弧放电形式表现出来。根据对换向火花研究表明,它是一种频谱广阔的电磁波,其频谱主要范围是30KHZ至1MHZ。换向火花的危害性应根据火花能量的标志,可以作为评价换向火花的标准。但由于火花测量十分复杂和困难,因而通常以火花亮度、密集程度和大小作为划分火花等级的依据。
世界各国对于火花划分标准各不相同,但是所有这些标准都是根据换向火花的亮度、密集程度、大小以及对电刷和换向器的损害表现,来划分换向火花等级的,由于至今尚未有某种仪器可精确测定换向火花等级,都是由观察者目视决定的,因而不可避免的带有火花观察者的某些主观因素。
(二)火花等级
GB755-87标准规定的火花等级,是用两种方法加以判别的。一是电刷下火花特征,即火花大小、亮度和密集程度;二是火花对换向器表面和电刷的损害程度。
在上述火花等级标准中可以看出,1级和11/4级火花是无害火花,11/2级火花虽然在换向器和电刷表面产生轻微灼痕,但仍允许长期运行,不致造成对电机的威胁;2级火花的电弧能量较大,会造成对换向器和电刷的灼伤,是有害火花,只允许在过载时短时出现;3级火花是危险火花,它能导致环火事故,不允许经常出现。
当直流电机采用晶闸管供电时,换向火花通常会比电池或机组大一些,原因是晶闸管供电电动机火花是含有交流分量,用眼睛观察到的火花亮度虽然大一些,但是实际上其电弧能量较小。
(三)火花产生原因
良好换向的前提是电刷与换向器之间稳定的滑动接触,主要是保持换向器氧化膜动态平衡,为此必须满足必要的机械、电气条件和适当的物理、化学因素。当必要的机械、电气条件不能满足,物理、化学因素要改变时,由于氧化膜动态平衡的改变,滑动接触变得不稳定,就会产生换向火花。产生换向火花的原因可以归结为下面几个方面。
1.电磁原因
如果换向元件内的合成电势不等于零,根据电磁理论,换向元件中产生的附加换向电流就会造成电刷前后刷边电流密度分布不均匀,电刷与换向片接触或脱离时,元件内换向附加电流并未为零,元件内的电磁能将以火花形式释放出来。延迟换向火花产生在后刷边;超越换向火花将产生在前刷边。
电枢绕组开焊或片间(匝间)短路都会造成电路上的不对称,亦将造成严重火花。
当电枢绕组为不对称多重绕组时,由支路间的电势不对称,在换向元件中产生一个脉动电势,将产生空载火花,负载时将加大。
电刷不在几何中心线上时,如换向元件进入主极区,换向元件因切割主磁通,将产生空载火花。
2.机械原因
换向器表面工作状态不良,如换向器突片或变形、片间云母片突出、换向器表面粗糙、电枢动平衡不好和电机振动等都将造成电刷与换向器之间无法保持稳定接触,而产生火花。电刷和刷握的工作状态不良,如电刷与刷握的间隙不合适、电刷压力不均匀、过大或过小、电刷材质不合适和刷握结构形式不合适德行,都影响滑动接触,也将产生火花。
3.电机负载及周围环境
电机严重过载时,由于电抗电势增加,换向极磁路饱和,电刷电流密度过大,换向火花将加大。冲击性负载、电流变化率过高将导致换向极磁通滞后,造成造成换向困难而产生火花。
当湿度太高或太低、温度过高或过低、周围存在油雾或有害性气体和含尘量过高等都会导致氧化膜平衡的破坏,无法形成正常氧化膜而影响正常滑动接触而产生火花。
产生火花的因素很多,而很多的因素又是相互影响的,在分析和检查换向火花产生原因时,必须根据实际运行条件来加以区分,以针对解决。
二、换向恶化原因的检查与处理
换向火花产生原因是多种多样的,必须在复杂众多的因素中,找到主要原因,针对性排除故障,恢复正常的换向。
寻找换向恶化原因的方法,通常称换向条件正常化检查,是直流电机换向事故处理最常用办法。其原理是这样的:一台直流电机在刚投入运行或过去一直运行,换向一直是正常的,而在以后运行过程中,逐渐变坏或突然恶化,说明电机在换向恶化前,其运行状态、滑动接触、电机结构和各部件工伯情况是正常的。在电机运行过程中,某些部件的工作状态发生了改变,从而破坏了滑动接触,改变了正常的换向状态,而导致换向的恶化。如果通过各种检查项目,对影响电机换向的机械电气条件和物理化学因素进行全面检查和调整,使其能恢复原来的正常状态,则换向也能恢复正常。
换向正常化检查是采用不同的检查方法,寻找换向事故原因并排除直流电机故障,通常包括下面几个项目。
(一)换向器片间电阻测量
当电枢绕组发生断线、开焊、匝间短路,或换向器发生升高片断裂、片间短路时,造成电磁上的不对称,将会产生换向火花。测量片间电阻就能发现电机是否存在上述故障。
片间电阻测量通常采用压降法,也可以采用专用片间电阻测量仪。
用压降法测量片间电阻时,把相等的测量电流依次通入两个相邻换向片,并用毫伏表测量通电两换向片间的电压降。如果电枢绕组和换向日历的焊接是良好的,没有短路开焊和断线,则全部换向器片间电压降应该相等(非全均压出现很小变化)。片间电阻测量得最大值或最小值与平均值之比,误差应不大于5%。测量结果如符合上述标准,说明电枢绕组和换向器存在开焊或短路时,则故障点所在的换向片间电阻值与平均值之间出现较大的差别,可以确定故障所的部位和性质。
如果电枢绕组是蛙绕组,由于在换向片之间构成了复杂的等值电路,当绕组并头套或换向器焊接有一处焊接不良或开焊时,片间电阻即会出现以极对数为周期的正弦变化规律,其中最高峰值即为故障所在位置。相反,当绕组和片间有短路点时,片间电阻正弱律变化的最低点即为故障所在位置。
在测量片间时,应注意以下几点:
1)测量时,电源电压要稳定,避免电压波动影响结果。
2)对于中、大型直流电机,必须用较大的电流(30~40A)通入换向片,才能较准确发现故障点。由于测量电流较大,送电棒和换向片脱离接触时必然会产生电弧,因此,测量最好在换向器非工作表面进行,以免破坏换向器工作表面。
3)测量操作时应注意,送电棒和测量不能直接相接触,以免损坏毫伏表。
片间电阻测量仪是测量片间电阻的专用设备。在事故抢修和现场测量时,压降法测量需4~5人同时操作,所需设备和仪器也较多,现场准备工作时间较长,有不便之处。现在国内已经研制成功了专用片间电阻测量仪。PD-1型片间电阻仪是根据压降法原理设计的。它由稳压器、调压器、整流器、测量回路和保护五个部分组成。
PD-1型片间电阻测量仪技术性能如下:
测量电流:0~50A连续可调。长期工作制30?,2h工作制40A,短时工作制50A。
测量精度:面板表头为1.5级;外接精密毫伏表0.5级。稳定性:电源电压波动±10%,输出电流变化小于±1%。外形尺寸:180mm×380mm×410mm。重量:16kg。
片间电阻测量仪大大减少现场测量的准备工作,也可减少现场测量的操作人员,已被不少单位采用。
(二)换向器摆度检查
换向器在长期运行后,由于云母材料中有机物的挥发产生收缩,紧固件的松动等使整体结构松弛而片间压力降低,产生变形和突片。当换向器变形或偏心时,在运行时将会使电刷跳动,滑动接触稳定性受到干扰,将产生机械性火花,严重时火花加大,换向器表面出现烧伤和氧化膜破坏,导致换向恶化。高速电机和多重路绕组电机的换向,对于换向器变形更为敏感。
当电机换向火花较,面且发现电刷跳动现象时,必须检查换向器摆度。
1.换向器摆度测量,通常有两种方法:
1)在低速运行或盘车时,可用千分表直接测量,在千分表的端头上套
上一个绝缘套,千分表座最好是磁吸式的,吸牢在铁板制成的基座上。根据电机盘车时千分表指针摆动范围,和换向器对应部位,即可测得换向器摆度和确定突片位置。
2)对于无法盘车和低速运行的电机,换向器的摆度可用测振仪来测量,先将测振仪进行校准,在测振探头--拾振器的探杆上,套上一个绝缘套,可用手持或用套圈固定拾振器,使之接触电刷压板或刷握的压指,即可从测振仪读得换向器摆度,如果将测振仪的输出接至示波器或记录器,即可以读得变形数值并观察振动波形。
用测振仪测得的换向器摆度有时会有一定误差,这是由于电机在高速转动时,电刷的起伏幅度中,不仅有乳白色向器的摆度,还包括了电刷的惯性跳动。
2.允许摆度
在测量摆度时,应区分是换向器变形和偏心,还是凸片(或凹片),
当换向器由于变形和偏心造成摆度时,在电机旋转时,摆度是逐渐过渡的,换向片之间径向的变化梯度较小,电刷的随从性较好。
由凸片(或凹片)造成的换向器摆度,其换向片局部位置在半径方向的变化梯度较大,电刷随从性不好,易引起电刷跳动,对滑动接触的影响较大。根据运行实践,凸片(或凹片)数值δm应限制在下列范围:
vk≥40 m/s δm<0.01㎜
15m/s≤vk<40 m/s δm<0.02㎜
vk <15m/s δm<0.05㎜
当换向器摆度超过额定值时,换向器必须进行车削.
(三)电刷中性面的检查
直流电机电刷中性线位置,一般应严格在主磁极几何中心线上,对于大型电机、可逆运行电机和高速电机尤其是如此。因为当电刷偏离主极中性线时,换向将发生超前和延迟。纵轴电枢瓜使电机的外特性发生变化,对可逆转电动机来说,两个转向下转速不同,而且外特性也不同,两个转向时换向强弱也不同。在电刷偏离中性位置较大时,由于换向元件进入主极磁通区,电机将产生空载火花。
电刷中性面检查方法如下:将全部电刷筛起,在励磁绕组出线端上连接一组蓄电池和一个刀闸开关。再用一个毫伏表依次测量相隔一个极距的换向片,当切断和合上开关时,毫伏表上指针将要摆动,毫伏表读数最小位置所对应换向片位置,即为电刷中性面的位置。
在中性面确定后,将刷架或刷焊座圈固定螺钉松开,移动刷回使刷握中心线与中性面对正,此时再紧固固定螺钉,并用漆在机座与刷上做好标志。
应该注意的是中性面检查应在极距、刷距调整后进行,以减少误差。
(四)极距、刷距和气隙的检查与调整
直流电机各排电刷之间的距离,主极之间和换向极之间距离应力求相等。因为刷距和极距不等则会造成各排电刷下被短路的元件在磁场中的位置不一样,换向极磁场和换向元件电抗电势波形不重合,造成电磁上的不对称,各个刷架下火花不等会使电机换向不正常。
1.刷距检查与调整
刷距鸡误差通常为±0.5㎜,一般用铺纸等方法来检查和调整
方法如下:首先将电机上一排刷架电刷位置调整好,使这排电刷边缘正好与一个换向片边缘相重合,然后在换向器表面铺一张纸,在接缝处做好搭接标记后取下,将纸以极数进行等分。划好等分线后,再铺在换向器上,使调整好刷焊和刷握垫片,使每个刷架刷握中电刷的边缘正好压在一条等分线上,再将全部电刷落下,电刷边缘与等分的距离就是刷距等分的误差,如将全部电刷按等分线调整,则可要纠正刷距误差。应该注意,在调整刷杆和刷握垫片时,应使刷握离换向器表面距离符合要求。
2.极距检查和调整
由于磁极固定螺钉在运行后松动,极距分布将出现误差,极距允许误差为±0.75㎜。极距较准确的测量一般采用磁极极靴上划中心线,再用游标卡尺和卡钳等进行测量,可以得以较精确的结果。当电机装配完后,电枢不能抽出的情况下,可以用卡钳测量极靴边缘之间的距离,也可以测量出极距等分误差。
3.气隙检查与调整
直流电机各主极和各换向极与电枢间隙δ必须均等,如气隙不均,则各极下磁阻不等,在相同的励磁磁势下,磁通量不相等,在部分刷架下火花就会较大。同时,由于主极下磁通量不等,还将出现电枢绕组内环流和单边磁拉力,当电机运行后,由于机座变形、轴承磨损等原因,均会出现气隙不均问题。
为使定子和电枢间的空气隙沿圆周各点均匀,设计规定允许偏差如下:
δ≤3㎜ Δδ为±10%
δ>3㎜ Δδ为±5%
气隙测量可采用如图5-18a所示方法:
(1)用塞尺测量 通常用于δ<10㎜小型电机情况。
(2)用专用气隙斜面塞尺测量 通常用于δ=5~15㎜气隙允许的电机中,测量比较方便。
(3)用气隙垫块和塞尺测量 气隙垫块可以加工成固定厚度,再用塞尺测量垫块和极靴之间的气隙值,这种方法通常用于气隙较大的电机。
气隙测量时应注意以下几点:
1)极靴和电枢表面漆膜必须刮去,测量处必须直接接触电枢和极靴叠片。
对于大中型直流电机,要防止铁心不圆度和转轴弯曲造成气隙值偏差,为得到准确的气隙平均值,应将转子位置每次盘车90°,共四次
(五)电刷与刷握工作性能检查
1.电刷弹簧压力的调整
合适的电刷压力是保持滑动接触的重要条件,电刷压力过小,造成电刷跳动和接触压降不稳定;压力过大则可能造成电刷机械磨损增加,换向器温升增高,电刷压力不均匀,风吹草动会造成各电刷之间电流分布不匀和个别电刷的火花。
电刷弹簧压力一般应保持在职16~24kPa范围内,而且电刷间的压力差不超过±10%。电刷的压力与电刷材质和换向器表面圆周速度有关,应合理选定。
电刷弹簧压力测定方法如下:用弹簧称在电刷提起方向勾起电刷压指,在电刷下垫一纸片,当纸片能轻轻被拉出时,弹簧称的读数,就是电刷弹簧压力。
2.握间隙检查
电刷与刷握之配合应保持一合适间隙并应符合一定公差。间隙过大,电刷在刷握内晃动,影响接触的稳定,有时还产生"啃边"现象;但间隙过小时,影响电刷在刷握内的自由滑动,甚至被"卡死"。
3.刷握离换向器表面距离的检查
由于刷架和刷握固定螺钉的变形,刷握离换向器表面距离将会发生变化。刷握离换向器表面距离应保持在2.5±0.5㎜范围内。
刷握离换向器表面距离与电刷应保持一定、这对防止振动有很大关系。双斜刷握与换向器表面距离,还影响电刷宽度,当距离过大时,电刷还将产生"顶角",影响工作。刷握距离可用厚度为2~3㎜的绝缘板打进行检查,当距离超过允许值时,可用2.5㎜厚绝缘板垫在刷握下,作为调整基准进行调整。
4.电刷材质和镜面检查
电刷型号是还符合要求,镜面是否出现异常,在换向火花较大时是必须检查的。电刷是构成滑动接触的主要部件,电刷材质和工作状态对换向有很大关系,因电刷牌号不合适或工作状态不正常,将影响滑动接触,或造成换向恶化。
一般说,不同型号的电刷,最好不要混用。电刷镜面在换向正常时是平滑光亮的。换向火花较大时,就会出现雾状和灼痕。当电刷中含有碳化硅和金刚砂等杂质时,镜面中就会出白色斑点或在旋转方向留下细沟。湿度过大或有酸性气体,电刷表面将出现镀铜现象。
(六)换向器表面工作状态的检查
换向器表面工作状态是保持良好滑动接触的重要因素之一。换向火花较大时,必须检查换向器表面状态,换向器片间云母二刻质量不好,云母片突出或粘附在云母光两侧,换向片倒棱不直均会引起换向火花;换向器条纹、斑纹都会使换向火花加大;云母沟中积存碳粉和换向片挤铜产生铜毛刺都会产生换向火花和闪络。如果发现上述现象,必须立即清理换向器表面,使其工作状态恢复正常。
有害的换向火花会造成换向器表面的烧伤,除一般烧伤外,有时会出现有规律的烧伤,通常烧伤的规律有重路数型、极距型、槽距型等,这时必须分析换向火花产生的电磁原因,根据存在问题加以解决。
(七)电机振动的检查
电机振动也是造成滑动接触不稳定的一种因素,是换向不良时需要检查的项目之一,换向火花大时,通常需用测振仪检查电机轴承、机座和刷架等部位的振动值,看是还超过允许值。如果振动值超过规定的允许值时,则需用快速福里哀分析仪(FFT)进行简单的频谱分析,从频谱主要成分分析中寻找振源,并采取必要的消除振源或减振措施。
(八)补偿绕组和换向极绕组极性检查和匝间短路检查
补偿绕组和换向极绕组的主要作用,一是抵消电枢反应减少主磁场畸变;二是产生换向电垫,抵消换向元件中的电抗电垫。当补偿绕组和换向极绕组极性接反时,则电抗电垫不公不会被抵消,而且由于换向电垫的叠加而增加了换向的困难。当补偿绕组和换向极绕组极性错误时,直流电动机表现为小负载情况下即出现火花,随着负载增加换向火花迅速加大,而空载时火花立即消失。极性错误一般发生在电机修理后,其检查方法通常可按图纸核对,检查接线是有误。另一种方法可使绕组通电,用磁针来检查绕组极性。
当补偿绕组和换向极绕组出现匝间短路时,由于换向电势的减少不能抵消电机电势,将会出现严重的延迟换向而产生火花。对于小型直流电动机的换向极线圈匝间短路,一般可用压降法检查,对于大型直流电动机补偿绕组和换向绕组的匝数很少,而电阻值极少,只能用外观检查,对短路处一定会出现表面绝缘榉变色和放电痕迹,根据这些现象即可发现故障所在并进行排除。
通过换向正常化检查,一般说大部分的换向故障可以检查出来,并加以排除,但是如果通过上述检查后,换向恶化原因依然没有解决,这时必须进行直流电机的无火花区域试验
三、环火事故与处理方法
环火是恶性事故。直流电机在运行中由于片间累积击穿,换向严重化,或特别恶劣的负载条件,均会出现正负极性刷架之间电弧飞越,环绕换向器表面出现一圈强烈的电弧,并伴随着强烈的弧光和巨响,这种事故称为环火。在环火发生极短时间内,电弧的高温和巨大能量,不仅对换向器和电刷装置造成严重破坏,而且对其他绕组也会造成不同程度损害,由于环火接地而产生轴电流还会使轴颈和轴瓦出现麻点和蚀痕。环火的巨响和强光还会使机旁维护人员受到伤害。因而在运行维护中必须要尽一切可能消除环火发生的隐患。
(一)环火产生原因
1.片间击穿
当换向器片间电压较高,而运行中又产生过电压,由于片间累积击穿,会产生环火。而更多的情况是由于换向器维护不良,清扫不认真,在换向器云母沟中积存了碳粉、铜粉和油污,或由于电刷挤铜,换向片铜毛刺延长导致相邻换向片的短路,这些导电物都构成了换向器片间云母沟中的导电桥,当这一导电桥随电枢旋转而进主极区时,换向器表面电位梯度增大,通过电流逐渐加大。当电流产生电动力超过维持粉末定位的力时,粉末构面的导电桥就会错位,导电桥由于熔化灼热而产生片间闪络。如果导电桥断裂点的有效电压超过电弧最低电压,就产生电弧。当断裂部分宽度增加到云母沟宽度时,维持电弧的电压也需增加,否则电弧将熄灭。当片间电压和起弧时感应电压大于维持电弧电压时,电弧将继续燃烧。电流随着换向片击穿而增大,磁场区域也增加,片间电弧沿换向器表面扩展过程。
当换向器相邻的换向片K和L因存在电位差,而片间存在导电物质时,导电桥断裂而产生电弧。在电弧作用下,由于导电物质的气化和电弧的灼热,造成了换向片K和L之间区域的空气局部游离成一个离子区。在这个区域内,由于电离气体内压力和电动力的作用,换向器的旋转电弧沿着换向器表面扩展至M。
如果电弧扩展的两个换向器片K与M之间的电位差,能维持片间电弧而不熄灭,则电弧将继续扩展。在一定条件下,片间电弧可以扩展到正负两个极性刷架之间,而取终造成环火。
2.严重的电刷火花
刷火花是导致换向器环火的加一个主要原因。当直流电机在恶劣的负荷条件下,换向器表面接触受到严重破坏时,就会在电刷与换向器之间产生严重火花。当换向器火花大到一定程度时,火花能量将引起电刷和换向片的燃烧和气化,并在燃烧区造成一个等离子区域,而这个电弧又被旋转的换向器沿电刷磨道所拉长。当这电弧被拉到一定长度的某一换向片M时,电弧是否能继续燃烧,就决定于换向器表面电位分布曲线和电弧特性。当换向片M的电位VKM小于电弧维持电压Ug时,电弧将熄灭。当VKM大于电弧维持电压Ug时,电弧奖持续燃烧,并将继续延伸。电刷磨道上空气的电离使为电弧延伸创造了条件。当换向火花能量大到某一量级时,电弧将伸展到异极性电刷上,而造成环火。
(二)环炎事故的处理
环火事故必定造成直流电动机的严重损害,首先应检查受损部位和程度,根据检查结果和受损程度来确定修理方案。
环火事故程度一般有三种情况。
较轻的环火事故。一般是电机容量较小,转速较低,环火发生时快速开关或自动开关很快动作,切断了主回路和励磁回路,电弧很快被短路电流磁吹作用所熄灭。这种环火一般只是烧黑了换向器表面和烧断个别刷辫。
较重的环火事故。电机容量较大,而转速较高,环火时虽然快速开关或自动开关及时动作,但是短路时电弧能量较大,所以损坏程度较重。这种环火可在换向器表面产生深浅不等的烧灼点,换向器外端部出现部分烧灼点,部分刷握被烧熔或烧损,刷架、导电环或定子绕组也会局部受损,熔化铜的喷溅,气化了的铜和碳结晶微粒附着绝缘表面,往往使表面泄漏电流大大增加,绝缘电阻降低为零。
严重的环火事故一般发生在高速和大容量直流电机上,除本身外特性曲线较硬外,由于保护系统接线错误和开关动作不及时等,将会造成十分严重的损害,此时电机必须大修,并重新制作换向器。
检查受损部位和程度:
1)检查绝缘电阻。环火事故后,必须将烧黑的换向器重新打磨,绕组吹风清理后用兆欧表检查各绕组绝缘电阻,是否符合GB755-87规定,以决定绝缘是否需要处理。
2)测量片间电阻,以检查升高片和电枢并头套是否出现开焊和片间短路现象。
3)检查换向器表面的受损程度是否表面氧化和积碳发黑,或是由于电弧烧灼面出现点状凹陷,还是出现了端部局部烧损或深度大面积烧蚀。
4)检查电刷和刷握的受损程度,刷握和电刷烧损数量以及必须更换的数量。
5)检查刷架和导电环是否出现缺损和需要修补更换的部件。
6)检查主极绕组、换向极绕组和补偿绕组。通常这些绕组是由于铜和碳蒸气的蒸熏而降低绝缘电阻,严重时也会使绕组受损。
7)检查电枢绕组和升高片。由于铜和碳的蒸熏和喷溅,以及环火时电枢绕组内部流过巨大的短路电流,必须检查绝缘电阻和片间电阻。
8)轴瓦的检查。环火后流经轴承的强大轴电流会使轴颈和轴瓦接触面上出现严重麻点,甚至使巴氏合金熔化。
9)轴承和定子固定螺钉的检查。环火时产生巨大的短路力矩。有可能使这些紧固件松动。
(三)环火事故的处理
1)换向器的处理。对于表面发黑的换向器,可用砂纸或换向器磨石等进行清理性的打磨;对于表面出现轻微和较浅灼点的换向器,可用换向器磨石进行一次打磨;对于烧灼较严重的换向器,必须重新车削外圆;烧灼严重无法修复的必须重新制作换向器。在打磨和车削换向器后,必须重新进行换向器的倒棱和下刻。处理后必须进行一次片间电阻检查。
2)更换烧损的刷握和电刷,电刷牌号必须和原来相同,电刷压力亦需调整均匀。
3)对于受损的绕组和其他部件进行焊补或更换。
4)绕组及导电部件表面绝缘层处理。如绕组及导电部件表面绝缘仅受蒸熏而绝缘电阻下降时,可用棉纱醮少许汽油、酒精和四氯化碳等溶剂,擦洗去这些部件表面凝聚的碳和铜微粒,再测量绝缘电阻。当擦洗清理后绝缘电阻仍难恢复,这时应考虑清洗整台电机的处理方式了。当表面绝缘层被电弧烧焦时,需剥去被烧灼绝缘层,重新绝缘处理。处理后绝缘电阻必须高于允许标准。
5)轴瓦处理。当轴瓦上出现较轻轴电流烧灼点时,轴瓦经研刮后可继续使用。当烧灼点密集和很深时,应更换备品轴瓦或重新浇铸轴瓦。轴瓦处理时,必须检查轴承座的绝缘层是否正常。
6)定子和轴承座固定螺钉如有松动,必须重新紧固。
(四)防止环火的措施
由于环火发生的时间很短,而且又在电机内部发生,所以很难用继电保护、空气开关和快速开关来保护。必须从设计和运行维护上采取措施解决。防止的措施有:
1)采用补偿绕组,直流电机加设补偿绕组后,首先是解决了换向极饱和问题;同时由于补偿绕组抵消了横轴电枢反应,因而解决主磁场畸变,从而使换向器电位分布曲线较为平滑(因为换向器表面电位分布曲线实际上就是气隙合成磁场的空间分布曲线的积分)。采用补偿绕组有利于抑制电刷火花和片间电弧的扩展。对于无法采用补偿绕组的小型电机,最好采用不同心气隙,也可以适当减少气隙磁场的畸变。
2)改善换向器表面处理,特别是换向片的倒角和片间云母的下刻质量,以及消灭换向片上存在的端部尖棱、夹角,这是有效防止环火的措施。
3)设计时,适当降低片间电压。对于大型电机片电压最好不高于16V;对于小型电机,不超过18V。对于片间电压较高,经常发生环火的电机,应适当降低过电压保护值。
4)加设隔弧板。在刷架之间的空间,用耐弧材料做成隔板进行挡隔,其作用是起电弧扩展的机械性障碍和减轻环火造成的损害。
5)加强换向器的维护。经常清理、擦抹和吹风,防止片间积法,防止片间铜毛刺产生,是防止环火发生的有效措施,特别是换向不好而发生过环火的电机,更应回强换向器的运行维护。
四、产生换向故障的原因和处理方法
换向是一个复杂的物理和电化学过程,它和电机本身及外界很多因素有关,而换向不良又表现在很多方面,如换向火花。氧化膜破坏、电刷与换向器磨损、滑动接触稳定性的破坏等。当换向恶化时,各方面的因素又相互影响,表现是错综复杂的,往往一个原因就会造成几种换向不良征象,有时几种故障原因,反映了共同的换向不良片象,为了便于现场解决和处理换向问题,下面将较详细地逐个分析几种换向故障原因,故障发展和处理方法。
(一)氧化膜异常
1.氧化膜形成和性质
直流电动机在运行过程建立起的氧化膜,是滑动接触中的一个重要因素,在换向器表面形成有光泽而且颜色均匀的氧化膜,是良好换向的前提。
氧化膜的形成主要是由于电刷和换向器之间滑动接触所发生的电化学过程。在大气中普遍存在水蒸气,电刷和换向器亦都覆盖一层极薄水膜,当电机运行时,电刷和换向器械之间电流通过并发生接触传导时,分别成为两个电极。当换向片是阳极时,水电解的氧离子趋向阳极,使铜被氧化成氧化铜和氧化亚铜。同时因机械和电气磨墨结晶不断堆积在铜表面,形成了厚度约为4~50㎜的氧化膜。其表面又吸附了氧气和水气,形成一水膜。因此,氧化膜成分中,包含有氧化铜、氧化亚铜、石墨、碳粒、少量其他杂质以及被吸附的水气和氧。电刷与换向器接触微观状态。
氧化膜是处于一种动态平衡过程中。由于换向片是不断回转于不同极性电刷之下,当换向片是阳极时,铜被氧化,氧化膜厚度增加、电阻增加;当换向片是阴极时,氧化铜又有部分被还原,氧化膜的电阻就减少。氧化膜上的碳颗粒与石墨不断堆积,又被负电刷的清理作用不断的磨去。 这们氧化膜在直流电机运行过程中不断的形成,也不断被破坏,经常地维持一种动态平衡。
氧化膜对于滑动接触是十分重要和有益的。首先使电刷与换向器之间磨擦系数减少,起很好的润滑作用,使电刷能稳定接触,减少了电刷的磨损。其次由于氧化膜电阻率大,增加了电刷与换向器间的接触压降,能限制被电刷短路元件内的短路电流,改善了换向。另外,由于氧化膜的硬度高,使磨损减少,能延长换向器的寿命。因此,正常的氧化膜是直流电机正常运行所不可缺少的。
氧化膜的颜色是各不相同的,通常是紫色的、红褐色的、浅兰色的、咖啡色的、灰色的德行,只要有光泽,颜色均匀都是属于正常的氧化膜。直流电机生成不同颜色的氧化膜主要取决于运行条件,如负荷、电机转速、电刷牌号、温度、湿度、换向火花等,当电机运行条件改变时,由于氧化膜原来平衡过程破坏,在新的条件达到新的平衡,氧化膜状态和颜色也会随之改变。
2.氧化膜异常和处理方法
1)氧化膜极薄现出铜本色,同时出现换向器的异常磨损。产生这种现象有如下原因:电刷牌号选择不合适,换向火花较大,且建立的氧化膜性能差;空气温度低,不利于形成氧化膜;电刷与换向器接触面上有硬度较高的研磨性尘埃,或电刷含有金钢砂和碳化硅。处理方法是选用形成氧化膜能力较强的电刷、适当增加湿度以及加强换向器的清扫和维护。对于建立氧化膜困难的直流电动机,可以采用人工建立氧化膜方法,建立起初始氧化膜后再投入运行。
2)氧化膜黑色而无光泽。通常称氧化膜过厚,常见的原因是空气中有油雾或换向器沾有油污,周围存在H2S、SO2、C1等气体。处理方法是消除空气中的油雾和有害气体,并用柔性换向器磨料或换向器修磨面,轻微磨去过厚氧化膜,当电机必须在上述环境中运行时,可以选用具有一定研磨作用的电刷,以适当减少氧化膜的形成。
3)氧化膜斑纹。在换向器上形色调不均匀的氧化膜,有时又会出现块状斑纹。产生斑纹的原因很多,常见的原因有:电机长期过载、堵转,换向器温度过高;换向器表面状态不良,电刷与换向器接触不稳定而产生换向火花;刷握排列和安装不正确,电刷与刷握配合不合适,电刷弹簧不均匀;电刷表面镀铜等都会产生器换纹。消除换向器斑纹通常办法是仔细调整刷握和电刷工作状态,认真处理换向器表面,为换向器和电刷的良好滑动接触创造条件。其次是减少过载和堵转,设法降低换向器工作温度,选用合适的电刷和减少换向火花。
3.氧化膜的维护
氧化膜是一种性质活泼,处于动态平衡过程的物质,直流电机氧化膜形成能力主要是决定于电机换向性能、负荷性质、电刷性能、周围介质和滑动接触状态。氧化膜变化过程往往是换向恶化的前兆,为此,必须精心加以观察和维护,经常地清吹和擦净换向器表面,当氧化膜状态发生变化时必须分析和找出影响因素。对于难于建立氧化膜的电机可以采取一些措施,促使建立氧化膜;对于氧化膜过厚的,则必须适当的清除一些氧化膜;对于不均匀的氧化膜和斑纹要清除后重新建立氧化膜。
4.清理氧化膜新材料
在采用砂纸打磨换向器时,必须要选用粒度较细的水磨砂纸,操作时先将砂纸包在一长方木块上,然后用木块轻压在换向器表面,在电机旋转时将木块沿换向器长度方向缓缓移动,即可对换向器表面起砂光作用,砂光后必须用压缩空气吹净铜粉和砂粒,并检查换向器表面粗糙度和云母沟中是否沾有铜粉等残留物。砂纸打磨的缺点是破坏了换向器表面氧化膜,因此,进行操作后必须重新建立氧化膜。
(二)换向器表面烧伤
持续的有害火花必然会导致换向器表面氧化膜的破坏,并在表面留下黑痕或灼痕,不能用溶剂擦去,这种现象通常称为换向器烧伤。当换向器出现烧伤后,由于氧化膜和滑动接触稳定性的破坏,将发生换向的恶性循环,所以当发现换向器表面烧伤时,必须立即处理。换向器烧伤有不同形式,产生的原因也错综复杂的,下面分析几种烧伤的征象。
1.换向器烧伤的几种征象
(1)表面普遍烧伤 于持续的有害火花,使整个换向器表面出现黑痕和灼点,表面粗糙。从换向片上观察可分以下几种情况:
1)换向片中间的灼痕。通常是由于换向器打磨不良,造成每一换向片表面曲率半径和换向器曲率半径不等,产生换向火花造成的。
2)换向器棱边上的灼痕,通常是换向片倒角不良,云母突出等原因产生的。
3)换向片的灼痕由边缘开始产生,逐渐向片中间扩展,通常是有害火花造成的,随着灼痕的扩展,整个换向片表面出现了烧伤。
(2)局部烧伤 换向器表面一个区域内出现了烧伤,其范围可由几片直至半个换向器表面。这种现象一般是由于换向器出现偏心,变形或局部突片造成的。
(3)有规律的烧伤 换向器表面有时往往出现一定规律烧伤,这种现象也称换向器烧痕,有如下几种类型:
1)槽距型烧伤。电枢槽内通常并列几种导体,即一个电枢槽内有几个绕组元件,亦称槽片数。槽距型烧伤是按槽片数为间隔出现的有规律烧伤。如某台电机的每槽内有三个元件,槽距型烧伤规律是每三片烧伤一片,顺序排列是1-4-7-10-13……。如槽片数u=4,则烧伤顺序是非曲直-5-9-13-17……。一般认为,被烧伤的通常是槽内最后一个元件所连结的换向片。原因是当槽内最后一个元件换向时,槽内其他元件已经换向结束,由于互感电势的作用,由电抗电势所产生的换向附加短路电流较大,这时易产生换向火花。
槽距型烧伤最始时只在局部区域内出现,随着换向火花加大而逐渐扩大到整个换向器表面,而且由每槽一片烧伤扩展到每槽两片或整个换向器表面烧伤。
过负载、电刷选择不合适以及换向极强弱调整不合适时,都会产生槽距烧伤。
2)极距型烧伤。在换向器表面有时会发生以极对数为间隔的烧伤。如四极电机,在换向器上出现对称两处烧伤;六极电机出现对称的三处烧伤,即其烧伤节距是K/p片。开始出现时是每组2~3片,以后逐渐扩展成每组十几片。极距型烧伤一般是由并头套开焊造成的。对于电枢为多重路绕组的直流机,由于机械和电气原因的干扰,如换向器突片,滑动接触不良、电刷电流密度分布不均,支路电流不均等也能造成极距型烧伤。
3)重路数型烧伤。换向器上出现按重路数为周期的烧伤,如双重路绕组的电机出现每二片烧伤一片现象;三重路绕组的电机出现每三片烧伤一片的现象。这种重路数烧伤规律是由于多重路绕组不对称性引起的,在换向过程中绕组间的不平衡电势在被电刷短路的换向元件中产生一脉振电势,在电刷附加换向电流中将叠加一脉振电流,而对换向产生干扰。当滑动接触不稳定时,这种干扰影响将更显着。电刷接触压降的大小对限制换向附加短路电流也是起十分重要作用。防止和消除重路数烧伤的措施是限制过负荷、建立良好氧化膜、选用合适电刷和加强换向器维护。
2.换向器表面烧伤的处理
分析原因针对处理,这是解决表面烧伤的前提。换向器表面烧伤是换向不良的直接反映。在处理前先要根据烧伤的不同征象来找出换向恶化原因并加以解决,否则即使修磨了换向器后,仍然出现烧伤。
轻度烧伤的处理:当换向开始恶化,并在换向片边缘开始出现黑痕和轻微灼痕时,这时可以采用轻轻修磨换向器办法,即能除去黑痕与灼痕。修磨材料可采用砂纸、柔性换向器修磨料和换向器修磨石。
(三)换向器不均匀磨损
换向器在运行中常出现轴向不均匀磨损和呈现波浪形磨损,这也是换向不正常和换向器异常磨损的反映,造成换向器不均匀磨损,通常有条痕和沟槽两种情况。
1.换向器条痕和沟槽形成
1)换向器条痕。条痕是指换向器表面出现了类似刀具切削的刀纹状的痕迹,有时深度可达2~3㎜,而且不均匀的布及换向器表面。虽然换向器表面高低不平,但氧化膜仍保持着。长痕的发殿过程开始电机有很小火花,在换向器表面圆圈方向出现了少量几圈微细刻痕,随着时间推延,微细刻痕逐渐变宽和变深,而且又产生新的刻痕,最后发展成严重的换向条痕,随之电刷和换向器磨损就迅速增加。
根据换向器条痕状态,又可分为连续条痕和弧立条痕。连续条痕是沿换向器圆周方向连续和均匀的刻痕;孤立条痕是不连续条状刻痕。
2)换向器沟槽。换向器沟槽是指在换向器表面出现与电刷宽度相近的光滑的磨槽,深度有时可达2㎜以上,沟槽产生初期仅在某些部位电刷磨道出现很浅的下凹,逐渐加深,并形成严重的沟槽,但是沟槽部位部位通常还覆盖着氧化膜,换向火花并不十分严重,有时甚至无火花运行。
在有些电机换向器上同时出现沟槽和条痕,或在沟槽内存在条痕。但不论是条痕或沟槽的出现,都将导致换向器的异常磨损。
2.产生原因和处理方法
换向器条痕产生原因很多,常见的原因是:电机长期轻载运行,电刷电流密度过低,换向器表面温度过低和周围空气湿度过高,将会使条痕很快发展;换向器表面油污染或周围环境中存在硫化氢、酸气、氯气等有害气体,易产生换向器表面的孤立条痕;电刷在制造过程中石墨化过程不够彻底,电刷材质中含有碳化硅等高硬度杂质,以及空气中含有耐磨性粉尘,则是条痕产生和发展的机械性因素。
换向器沟槽产生的原因主要是:电刷位移方法不正确,没有考虑换向器表面上电刷磨道的均匀覆盖和正负电刷下换向片磨损量不等的因素;其次,当周围环境中含有较多的耐磨性尘埃和电刷硬度过高等,也易产生换向器沟槽。
当换向器表面出现的条痕和沟槽深度超过1㎜时,一般应重车换向器。但是,同时必须采取措施,解决导致条痕和沟槽的各种因素。电刷位移本来是一种防止因机械和电气原因产生换向器不均匀的措施,对于因电刷位移不当而引起沟槽的情况,必须调整电刷排列方式,以实现合理的位移。
(四)电刷抖动
电机在运行过程中,由于换向器润滑不良等原因,会出现电刷的高频噪声,这种情况通常称为电刷的抖动。电刷抖动不仅使火花加大,而且往往导致电刷掉角、碎裂,刷辫脱落,严重时将刷握的压指断裂和铆钉脱落,使电机无法正常运行。
电刷的抖动产生直接原因是换向器与电刷的润滑情况不好,例如:换向器氧化膜过厚、电刷磨擦系数过大、空气湿度过低和电刷弹簧压力过大等都会造成高磨擦而导致电刷抖动。换向器表面状态不良,换向器变形、电刷与刷握配合过松或过紧,刷握固定螺钉的松动等机械性的原因亦可能导致电刷的抖动。
消除电刷抖动办法是分析和寻找出造成高磨擦原因和机械松动的部位,针对性的予以解决。如发现氧化膜过厚,可用柔性磨石或换向器清理石适当清除过厚氧化膜,并使其产生光泽;当空气湿度低于5g/m3时,必须适当用喷雾增湿;当电刷压力过大时,要适当调整压力;而电刷磨擦系数过大时,则必须选择润滑性能较好的电刷(如浸渍石蜡或权利脂的电刷)等等。
解决高磨擦的另一个办法是用润滑剂润滑换向器表面,如定期清擦换向器,并在表面涂石蜡,高频颤动和噪声就会显着降低,但这只是一个临时性的措施,不能彻底解决问题。
对于造成电刷抖动的机械性原因,必须仔细寻找和加以解决。
(五)换向片挤铜
直流电机在运行中,有时换向片边缘会出现铜毛刺,通常是在换向片边棱出现羽毛状的铜毛刺或铜箔片并逐渐延展出来,这种现象叫换向片挤铜。产生挤铜现象的原因是由于滑动接触情况不好,由于高摩擦和电刷抖动,使换向片表面受到一种高频锤击和定向挤压作用而表面蠕变,逐渐向旋转方向延展。氧化膜过厚,按向器表面的油污垢、电刷摩擦系数过大和空气湿度过低都是产生挤铜现象的诱发因素。挤铜现象大多都发生在单向运行的电机上。当换向片发生挤铜现象时.首先使氧化膜变得不均匀,在某些部位将出现铜本色的亮纹。由于铜的蠕变和延展,实际上换向片的曲率半径变得不均匀.云母沟中出现了铜毛刺,增加了片间短路和闪络的发生,严重时将导致环火事故,因此当发现铜毛刺时,必须立即进行处理。
对于出现挤铜的直流电机,通常作如下处理:首先对换向器进行倒棱,以剔除附在换向片棱边上的铜毛刺和铜箔,并根据换向器氧化膜和表面情况,可适当的修磨换向器。从根本来说,为防止挤铜现象必须避免高摩擦和电刷抖动。
(六)电刷"镀铜"
电刷镜面上有微细铜粉沉积.有时部分刷面呈铜色,这种现象叫电刷镀铜。在周围空气绝对湿度过大(超过20g/m ),或存在酸气时,因氧化膜表层水膜的电解作用加强,在滑动接触过程中就会使换向器的铜因电解的作用而趋向电刷接触面,细微的铜粉就会沉积在电刷镜面上,而造成镀铜。另外,在空气中存在耐磨性粉尘和油雾,换向器工作温度过高、片间云母突出和电刷磨损率太大等亦可能产生镀铜现象。
电刷镀铜会对电机换向带来很多问题。电刷镀铜往往直接导致换向器条痕,换向火花加大、换向器和电刷出现异常磨损。因此,当出现电刷镀铜时,首先必须修磨电刷和换向器表面,并认真清理碳粉和铜粉,使电刷和换向器恢复稳定的滑动接触。同时,也必须加强对换向器的维护,并采用过滤冷却空气,调节空气湿度等措施.保持氧化膜正常的动态平衡,可以防止电刷发生镀铜现象。
|